Comprehensive Guide to Downhole Filters in the Building Supplies & Machine Rental Industry
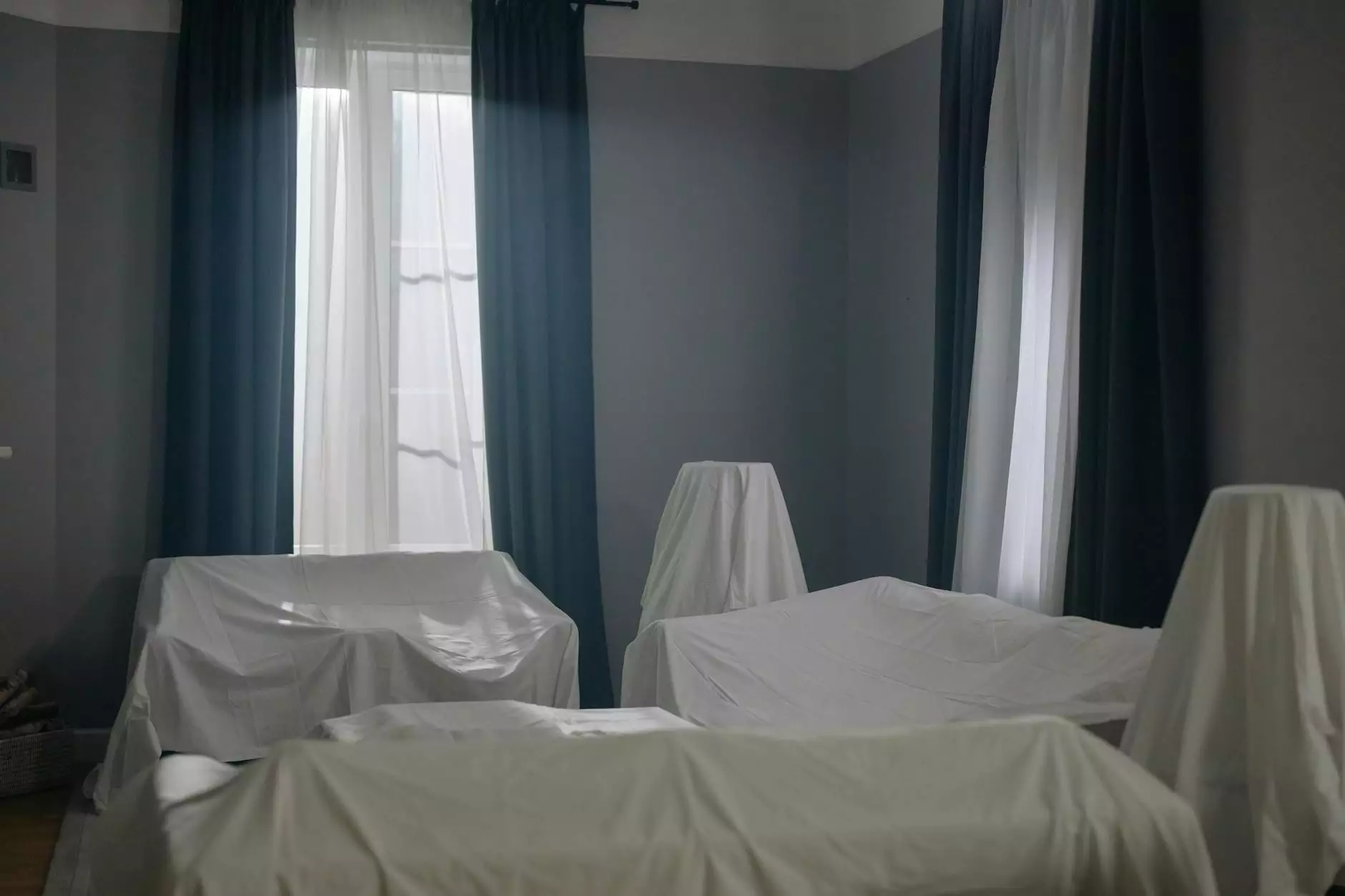
The building supplies and machine & tool rental sectors are fundamental pillars of modern construction and drilling operations. Among the many technological advancements that have revolutionized these industries, downhole filters stand out as vital components that ensure operational efficiency, safety, and environmental compliance. This comprehensive guide dives deep into the world of downhole filters, exploring their design, applications, benefits, and the critical role they play in modern drilling and construction projects.
Understanding Downhole Filters: What Are They and Why Are They Essential?
In the context of drilling and construction, downhole filters are specialized filtration devices installed at various depths within drill strings or boreholes. Their primary function is to remove unwanted debris, sediments, and particulates from the drilling fluid or mud as it circulates through the wellbore. This filtration process is essential to maintain optimal drilling conditions, protect equipment, and prevent costly downtime.
Effective downhole filters are designed to withstand extreme pressures, high temperatures, and the aggressive chemical environment typical of deep drilling operations. They are engineered to ensure that only clean, particulate-free fluid reaches critical components such as pumps, valves, and drill bits, thereby significantly reducing the risk of wear and mechanical failure.
The Role of Downhole Filters in Modern Drilling Operations
Enhanced Drilling Efficiency
By filtering out debris and particulates, downhole filters facilitate smoother drilling processes. Clean drilling fluids result in less wear on drill bits, enabling longer drilling intervals and reducing the frequency of bit replacements. This directly translates into lowered operational costs and increased progress in project timelines.
Protection of Equipment
Unfiltered debris can cause severe damage to sensitive equipment such as pumps, motors, and measurement devices. Downhole filters act as a barrier that prevents foreign particles from entering and damaging critical machinery, thereby extending equipment lifespan and reducing maintenance costs.
Environmental Compliance and Safety
Effective filtration minimizes the release of contaminated fluids and sediments into surrounding environments, ensuring compliance with environmental regulations. Moreover, clean drilling fluids contribute to safer working conditions for personnel by reducing hazards associated with particulate exposure and equipment failure.
Types of Downhole Filters: Tailoring Solutions to Specific Drilling Needs
The diversity of drilling projects demands a range of downhole filter solutions. Key types include:
- Inline Downhole Filters: Installed directly within the drill string or casing, these filters provide immediate filtration at the point of fluid circulation.
- Sand Screens: Used to prevent formation sand from entering the wellbore while permitting fluid flow, enhancing well stability.
- Disposable Filters: Designed for single-use scenarios where quick replacement is vital, offering convenience in maintenance.
- Reusable Filters: Engineered for durability, these filters can be cleaned and redeployed, reducing operational costs over time.
Material Composition and Design Innovations in Downhole Filters
Advancements in materials science have driven significant improvements in downhole filter design:
- High-Strength Meshes: Made from stainless steel or premium alloys, these provide durability and resistance to corrosion.
- Porosity Optimization: Fine-tuning pore sizes enhances filtration efficiency while maintaining adequate flow rates.
- Advanced Coatings: Anti-corrosion and sediment-repellent coatings extend the lifespan of filters in harsh environments.
- Modular Construction: Facilitates customization for specific operational needs, including various flow capacities and particle retention sizes.
Implementing Downhole Filters for Maximum Operational Benefits
Best Practices in Selection and Deployment
- Assessment of Drilling Conditions: Understanding geological formations, fluid properties, and temperature profiles guides the selection of appropriate filter types and specifications.
- Integration with Drilling Equipment: Compatibility with existing equipment ensures seamless operation and maintenance.
- Regular Monitoring: Installing sensors to track filter performance can preempt failures and facilitate timely replacements.
- Training and Maintenance: Proper operator training ensures the correct handling and servicing of downhole filters.
Case Study: Enhanced Deepwater Drilling with Downhole Filtration
In a recent deepwater drilling project, engineers deployed advanced downhole filters to combat high sediment loads in the drill mud. The filters effectively prevented debris ingress into sensitive equipment, resulting in a 20% reduction in equipment wear and a significant decrease in non-productive time. This case exemplifies how tailored filtration solutions can dramatically improve project outcomes in complex drilling environments.
Choosing the Right Supplier and Maintaining Quality Standards
Partnering with a reputable supplier like Maverick Drilling ensures access to high-quality downhole filters built with precision and durability. Key factors include:
- Certification and Compliance: Look for ISO certifications and adherence to industry standards.
- Customization Options: Ability to tailor filters to specific project needs.
- Technical Support: Availability of expert assistance for installation, troubleshooting, and maintenance.
- Cost-Effectiveness: Balancing initial investment with long-term savings through enhanced durability and efficiency.
Future Trends in Downhole Filters and Filtration Technologies
The industry is witnessing exciting innovations aimed at further enhancing filtration performance:
- Smart Filters: Integration of sensors for real-time monitoring and predictive maintenance.
- Nanotechnology Coatings: Providing superior corrosion resistance and particle filtration capabilities.
- Eco-Friendly Materials: Reducing environmental impact with biodegradable and recyclable filter components.
- Automated Backflushing Systems: Enabling self-cleaning to minimize manual interventions and downtime.
Summary: The Critical Importance of Downhole Filters in Building & Drilling Industries
In conclusion, downhole filters are more than just components—they are essential enablers that underpin the success of modern drilling and construction projects. Their role in improving equipment longevity, operational efficiency, environmental compliance, and safety cannot be overstated. By leveraging innovative designs and high-quality materials, and collaborating with experienced suppliers like Maverick Drilling, industry professionals can ensure optimal filtration performance tailored to specific project demands.
As the industry continues to evolve with new technological advancements, the future of downhole filters is promising, with smarter, more efficient, and environmentally sustainable solutions on the horizon. Companies investing in these technologies position themselves at the forefront of innovation, efficiency, and safety in the building supplies and machinery rental sectors.
Final Thoughts
Understanding and implementing the right downhole filters are fundamental to successful drilling operations. From technical specifications and material choices to strategic deployment and maintenance, every aspect plays a crucial role in maximizing productivity and minimizing risks. Embrace the latest innovations and partner with trusted suppliers to leverage the full potential of downhole filtration technology.